NOVA Integration Solutions, Inc. (NIS) has developed a solution that is intended to detail your enclosure problems and to take the next steps in remedying these concerns with a new product offering known as our Enclosure Evaluation Service (“E-Squared”). If you send us your electronic enclosure or better yet send us your electronic files, NIS will perform a full analysis on your enclosure. The results will be summarized in a comprehensive report to include our recommendations in making any needed
changes.
The service will include a full mechanical, electrical and thermal assessment of your enclosure to determine where it can benefit from any change in the form of remedies and improvements. The service is ideally suited when:
- Performance improvements and new features must be added.
- Changes to minimize size, reduce weight and improve thermal management are needed.
- An expanded power supply is needed to include the use of an EMI power filter.
- A technology refresh is required due to poor product performance or part obsolescence.
- A prototype was developed and the design must transition to production.
- Documentation does not exist and the enclosure may need to be reverse engineered.
- Your enclosure must be re-evaluated to meet military-grade testing and specifications.
CASE 1: ATR Chassis Weight Reduction
Problem: An innovative way was needed to reduce weight in a hybrid-cooled ATR chassis. In doing so any improvement needed to be in the form of a drop-in replacement, sustained thermal conductivity and without loss of structural integrity. Any changes had to be in the form of a retrofit and utilize in future designs to provide lighter weight chassis for manned and unmanned aircraft (UAVs).
Conclusion: Solidworks was used to model the chassis resulting in the Recommendation to use a specially designed ATR chassis side plate consisting of a variety of thermally-conductive lighter-weight crystalline carbon fiber materials in combination with an aluminum shell. The improved side plate was designed to exceed all of the environmental requirements and was provided as a light-weight drop-in replacement.
The improved side plate was reduced in weight from 6.7 pounds to less than 4.9 pounds. Two side plates are used in the chassis resulting in a total weight savings of 3.6 pounds. Future changes are being considered to reduce weight in a similar manner and the concept developed by NIS known as Flatware is expected to expand.
The increased thermal management introduced by the new design may also result in the removal of fans that may no longer be needed.
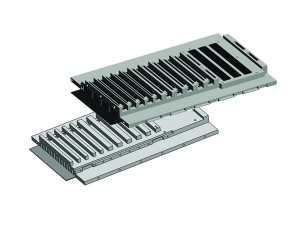
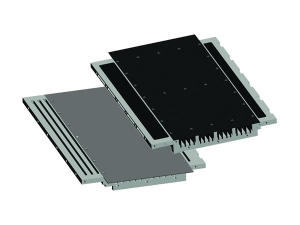
CASE 2: Technology Update – 7U VME64x Chassis
Problem: A technology update of a military-grade in-flight convection cooled enclosure was needed. The upgrade needed to incorporate a transition from VME to a VME64x backplane, utilizing higher-performing computer interfaces, an updated system monitor, the insertion of an EMI power filter and the replacement of the power supply in support of the aircraft’s 400Hz power input system. The upgraded chassis needed to be a drop-in replacement when installed in the aircraft and be fully backward compatible.
Conclusion: The Customer provided an existing chassis and the set of engineering drawings in support of the effort. The existing chassis was modeled using SolidWorks and redesigned to include the needed internal subassemblies. Airflow simulations were generated to validate the upgraded cooling system required by the additional boards and power usage.
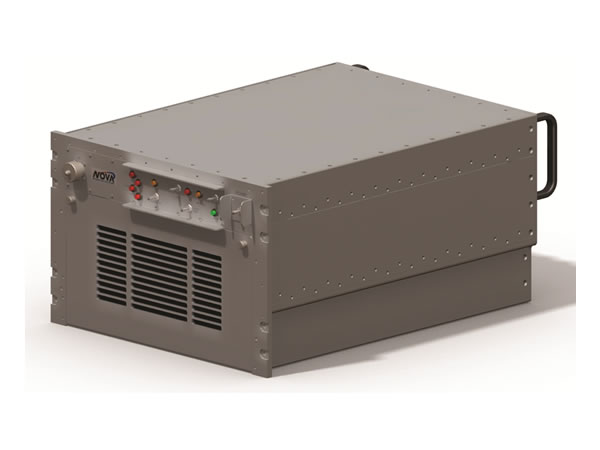
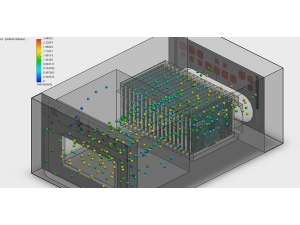

CASE 3: Amplifier Heat Sink Recommendation
Problem: The customer’s “Amplifier” enclosure was over heating and shutting down under normal operating conditions. An urgent evaluation of the enclosure was needed to confirm the problem to include a recommendation for an improved heat sink. The improvement required an inexpensive and quick solution that was easy to install.
Conclusion: Solidworks was used to produce a thermal analysis utilizing a variety of heat sink designs which resulted in the recommendation of an alternative heat sink. The recommended heat sink was a stock part available from at a local extruder and the instructions to easily retrofit their enclosures was provided by NIS.
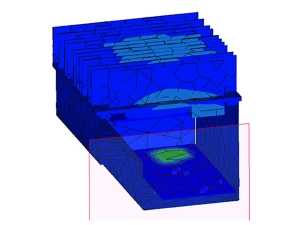
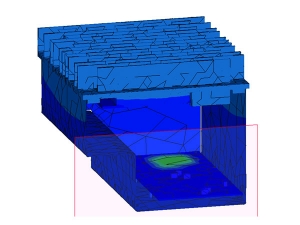
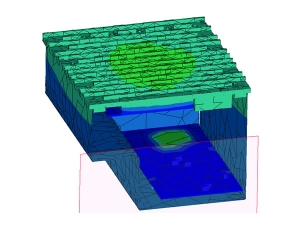